Don't lose any more money!
Complies with H&S NOM's for Hazardous Energy Control Part 1
Accidents are a factor that most companies have to deal with continuously. Even when the Health and Safety departments work to avoid them, they continue to present a high incidence rate every year. Many of these accidents are related to the use of industrial equipment that represents a constant risk for workers, mainly due to the energies that the equipment uses for its operation and production processes.
Hazardous Energies

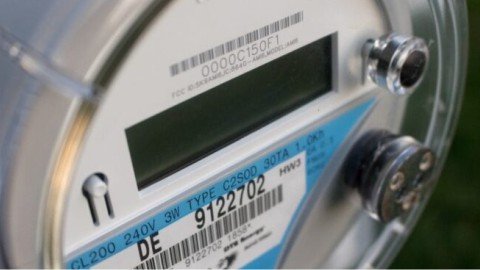
Energy is the capacity of a system to produce work, which can be manifested as electrical, magnetic, mechanical, thermal, chemical, potential, hydraulic, pneumatic, sound, light, radiation, among others. From a safety point of view, hazardous energies are defined as all types of energy that can cause harm to workers at the time of intervening in a piece of equipment.
In general, hazardous energies can be classified as follows:
- Electrical energy hazard: Electrical energy is present in electrical circuits with voltages and by accumulation of static energy, it can cause injuries associated with electrocution such as burns, damage to the nervous system, heart and respiratory failure.
- Mechanical energy hazard: It is energy stored or contained in the movement of mechanical elements that can cause crushing injuries, amputations, blows, cuts in any part of the workers’ body, mainly in the extremities.
- Hydraulic energy hazard: It is energy contained in pressurized liquid fluids driven by pumping systems and can cause injuries such as blows, amputations, cuts to any part of the workers’ body.
- Pneumatic energy hazard: It is energy contained in pressurized gaseous fluids driven by compression systems and can cause injuries due to expansive waves that can cause shrapnel of materials impacting any part of the workers’ body.
- Chemical energy hazard: Energy present in substances that present exothermic (heat release) or endothermic (heat absorption) reactions, these can be alkaline or acid substances that can cause injuries on contact, breathing vapors, eye exposure. Injuries can be burns, blindness, intoxication, among others.
- Thermal energy hazard: It is energy present in objects, substances or environments with high temperatures (from 60°C) or very low temperatures (below 0°C) that when in contact with them can cause injuries such as burns and dehydration.
Occupational Accidents
On average, 1,412 deaths occur in Mexico every year due to occupational hazards and 411,000 work accidents, which are the leading cause of temporary disability in the country and represent 81% of the risks registered by the Mexican Social Security Institute (IMSS).
The International Labor Organization (ILO) informed, within the framework of the commemoration of the World Day for Safety and Health at Work, that every day around 6,300 people die in the world as a result of work-related injuries or illnesses.
These statistics have remained more or less constant over the last 5 years, even with the efforts made by the different Health and Safety institutions in the different countries, and therefore, reducing accident trends represents an area of opportunity.
Employer Obligations
Within the labor relations, employers have as one of their fundamental tasks the obligation to guarantee the safety of the employee in accordance with the following:
Federal Regulation on Safety, Hygiene and Working Environment.
Art. 13. Employers are obliged to adopt, according to the nature of the work activities and industrial processes carried out in the work centers, the pertinent safety and hygiene measures in accordance with the provisions of these Regulations and the applicable Standards, in order to prevent accidents in the use of machinery, equipment, instruments and materials.
- To show to the labor authority, when so requested, the documents that this Standard requires it to prepare.
- Elaborate a study to analyze the potential risk generated by machinery and equipment in which an inventory of all factors and hazardous conditions affecting the worker’s health must be made.
In the preparation of the study of potential risk should be analyzed:
- The moving parts, heat generation and static electricity of machinery and equipment.
- The cutting surfaces, projection and heating of the raw material, by-product and finished product.
- Handling and condition of tools.
For any risk that has been detected, the following should be determined:
- The type of damage.
- The severity of the damage.
- The probability of occurrence.
Based on the study to analyze the potential risk, the employer must:
- Elaborate the Specific Safety and Hygiene Program for the Operation and Maintenance of Machinery and Equipment, make it known to the workers and ensure its compliance.
- Have trained personnel and a first aid manual that defines the procedures for emergency care.
Employee Obligations
Workers have the obligation within the work centers:
- Participate in the training provided by the employer.
- Comply with the measures indicated in the Specific Safety and Hygiene Program for the Operation and Maintenance of Machinery and Equipment.
- Report to the employer when the protection systems and safety devices of machinery and equipment are deteriorated, out of order or blocked.
- Use personal protective equipment according to the instructions for use and maintenance provided by the employer.
- Wear short or tied back hair, do not wear chains, rings, bracelets, loose sleeves or other objects that could be a risk factor during the operation.
- Report to the employer any anomaly in the machinery and equipment that could imply risk.
Regulatory Framework
The OSHA (Occupational Safety and Health Administration) Hazardous Energy Control (Lockout/Tagout) Standard (Hazardous Energy Control), Title 29 Code of Federal Regulations (CFR) Part 1910.147 (developed in 1989), addresses the practices and procedures necessary to deactivate machinery or equipment to prevent the release of hazardous energy during servicing and maintenance activities performed by employees. The standard describes the control measures for hazardous energy, whether electrical, mechanical, hydraulic, pneumatic, chemical and thermal, among other energy sources. In addition, 29 CFR 1910.333 establishes requirements for the protection of employees working with electrical equipment or circuits. That section requires workers to observe safe work practices, including lockout/tagout procedures. These provisions apply when employees are exposed to electrical hazards while working with or near electrically powered conductors or systems.
Over the years it has become an international benchmark for the control of hazardous energies in the workplace and gave rise to the manufacture of lockout and tagout devices.
The Secretary of Labor and Social Welfare (STPS) through NOM – 004 – STPS – 1999 indicates the obligations of work centers to perform risk analysis and establishes the use of safety cards and devices for the control of hazardous energies.
What are the consequences?
In the next blog we will talk about the consequences of non-compliance with the NOM’s mentioned above and how it affects costs. Click here to go to part 2.
Sources: STPS, OSHA, IMSS Estadísticas 2000-2018, CAREINTRA, IFAM, El Economista.
Comments
We are interested in your opinion, please leave us a comment